Scientists from Wrocław University of Science and Technology and Taiwan are working on new dental implants

Researchers at the Wrocław University of Science and Technology and the National Taipei University of Technology are developing dental implants made from 3D printed ceramic structures connected to a metal core. Thanks to the use of biodegradable magnesium, bone tissue will be able to gradually grow into such an implant.
According to a press release sent by the university, joint activities of teams from Poland and Taiwan are possible thanks to funding from the Polish National Centre for Research and Development and MOST (The Ministry of Science and Technology in Taiwan) for the CERMET project.
'The result will be a composite implant that can potentially replace a human tooth. Its scaffolding, made of aluminium oxides, is manufactured using the additive method (3D printing), which guarantees that it will be tailored to the needs of a specific patient,’ says the press release.
In the upper part (crown), the ceramic structure is solid, and in the lower part (root) it is porous. Thanks to this, it can be saturated with liquid metal - a magnesium alloy. This will reduce the fragility of the structure, and the core itself will initially act as an 'anchor', holding the implant in the jaw. Magnesium will gradually degrade, freeing up space for bone tissue to grow in (this process is osseointegration). As a result, the implant will become very stable - embedded in human tissue.
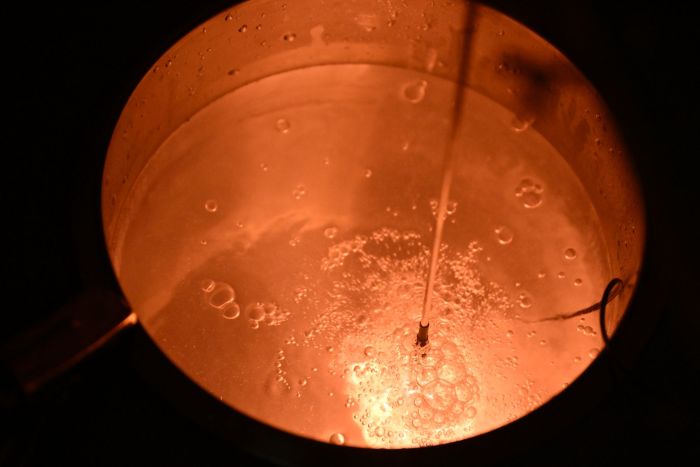
Scientists from Taiwan, in collaboration with researchers from Wrocław, develop appropriate ceramic preforms with open porosity, i.e. structures that, combined with a metal core, will form an implant. These structures are sent to the Wrocław University of Science and Technology, where researchers from the Department of Lightweight Elements Engineering, Foundry and Automation at the Faculty of Mechanical Engineering infuse them with metal - a biocompatible magnesium alloy.
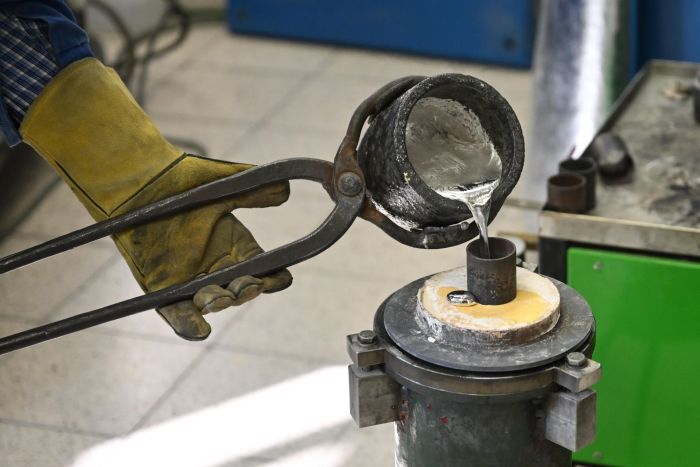
'We are in the early stage of our project, so for now we are testing two casting techniques and then we will choose the most advantageous one. The first is the pressure infiltration method, or more precisely pressing from the liquid state, in which a ceramic shape is placed in the press chamber and poured with liquid metal, and then, lowering the piston, we press the liquid metal into the porosity of the preform. The second technique is precision casting, also used in jewellery making. Here, we first create a plaster mould for a previously prepared wax or plastic model,’ says Dr. Anna Dmitruk in the press release.
Scientists from the Wrocław University of Science and Technology are also conducting a number of tests of implant prototypes, including strength tests, connection quality tests and thermal expansion tests, to check whether the materials making up the composite will not change their volume due to temperature changes, which may cause cracking, for example.
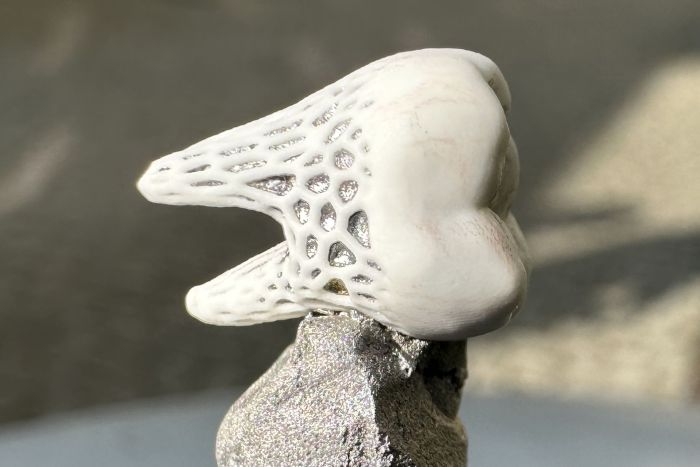
Implant samples are also subjected to a plasma electrolytic oxidation process, also called micro-arc oxidation. Thanks to it, the magnesium with which ceramic structures are saturated does not oxidize so quickly and its degradation process is gradual.
'Few units in Poland use with this technique. We place the sample in a tank filled with electrolyte. The sample and the other metal element of the system are the anode and cathode, respectively. We generate high electrical voltage in the system, which leads to the formation of plasma discharges on the sample surface. As a result, a thin porous coating of magnesium oxide is formed on it, with a thickness measured in micrometers. This coating has anti-corrosion properties and increases abrasion resistance, and in the case of the implant, its most important property for us is that it slows down the resorption of magnesium in the body,’ says the team’s Natalia Raźny.
Work in the CERMET initiative will continue for three years. The result will be an implant prototype. After it is developed, scientists can seek financing for subsequent stages of work, including pre-medical research.
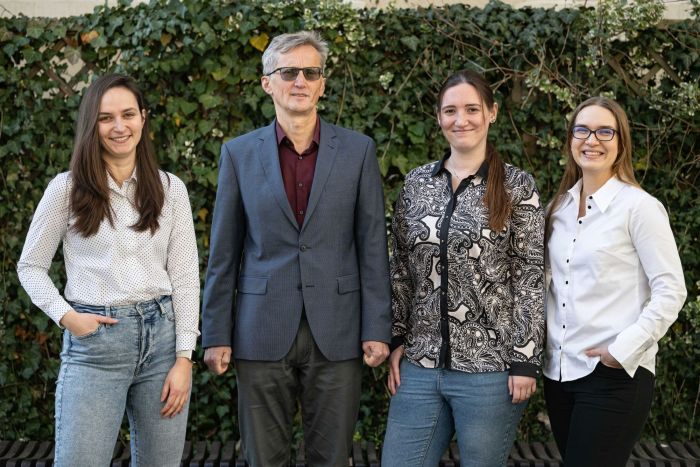
The project leader is Professor Krzysztof Naplocha from the Faculty of Mechanical Engineering of the Wrocław University of Science and Technology, and his team members are Dr. Anna Dmitruk, Dr. Adrianna Filipiak-Kaczmarek and Natalia Raźny. (PAP)
PAP - Science in Poland, Roman Skiba
ros/ agt/ kap/
tr. RL
Przed dodaniem komentarza prosimy o zapoznanie z Regulaminem forum serwisu Nauka w Polsce.